Vibration stress relief
Previously, for the stress relief of welded structures and pieces aging and the heat-treatment were used. The first one was time-consuming, and the second one costly. On our continent, even today the stress relief with heat-treatment is the prevalent method, which is reliable though, but has its limits. At the heat-treatment procedure the particles are wabbled by heating to restore them. The higher temperature there is, the higher frequence are the particles oscillating on. The americans have reversed the process a long time ago: they vibrate the piece itself, and the changing frequences of vibrations will relief the stress caused by the welding. The process is also true the other way around. We can apply it during or after the welding or after cutting or even after building back the part to its place.
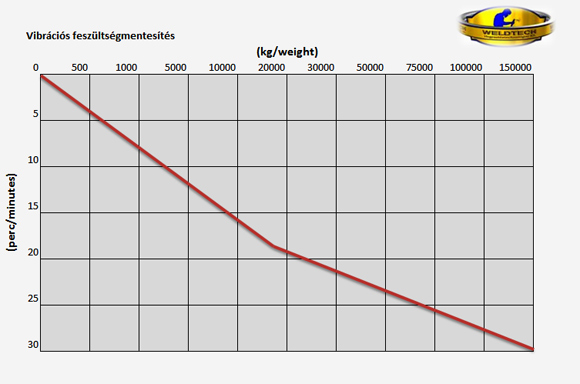
Advantages against traditional proceedings:
extremely cost-effective, the electricity consumption is minimal
fast (15-60 minutes) and can be performed also on site
there is almost no weight and size limit
the deformation, the size change and corrosion can be reduced to zero
the longavity of stress will grow
less porousity, deeper melt, minimal splash
conditioning the standard of the granule and of the seam
the danger of cracking reduces
the pre-heating before welding can be reduced or left out
the piece does not lose its hardness
We apply it mainly during the welding. At grey-alloys the demand of mechanical stress relief reduces to minimal, and the danger of cracking is minimal. Earlier we repaired (with welding) such parts, which deformed substantially. We had to align these parts, which increased the prices as well. Since we have been using this device, the deformation, the shrinkage are almost zero and we can perform also the sensitive reparations safely. Yearly, we are repairing a lot of such parts with layering-welding, which raw material is Duplex (bimetal) metal. For the sake of bigger wear-resistance the customer requested SuperDuplex material. This alloy doesn’t like the pre-heating so much. But because of the forming of the piece and the quantity of the applied material (40-70 kg) it was necessary and it deformated even this way, which we could correct only with additional applying and cutting. This problem reduced since the introduction of vibrational tension exemption to minimum. With its application, we can provide more cost-effective and quality service for our customers.